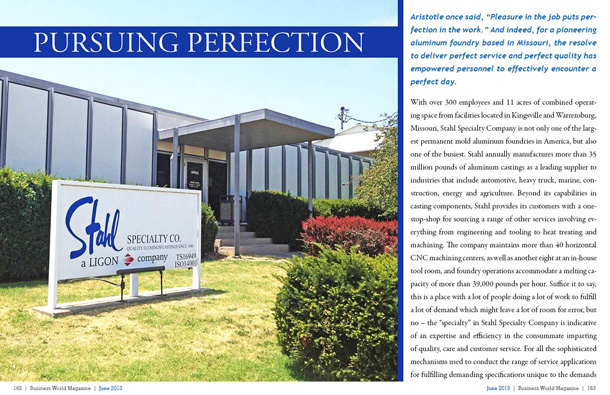
Â
Pursuing Perfection
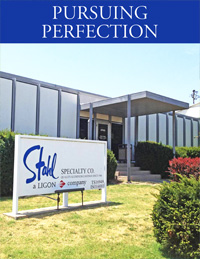
Aristotle once said, “Pleasure in the job puts perfection in the work.†And indeed, for a pioneering aluminum foundry based in Missouri, the resolve to deliver perfect service and perfect quality has empowered personnel to effectively encounter a perfect day.
With some 700 employees and 11 acres of combined operating space from facilities located in Kingsville and Warrensburg, Missouri, Stahl Specialty Company is not only one of the largest permanent mold aluminum foundries in America, but also one of the busiest. Stahl annually manufactures more than 35 million pounds of aluminum castings as a leading supplier to industries that include automotive, heavy truck, marine, construction, energy and agriculture. Beyond its capabilities in casting components, Stahl provides its customers with a one-stop-shop for sourcing a range of other services involving everything from engineering and tooling to heat treating and machining. The company maintains more than 40 horizontal CNC machining centers, as well as another eight at an in-house tool room, and foundry operations accommodate a melting capacity of more than 39,000 pounds per hour. Suffice it to say, this is a place with a lot of people doing a lot of work to fulfill a lot of demand which might leave a lot of room for error, but no – the “specialty†in Stahl Specialty Company is indicative of an expertise and efficiency in the consummate imparting of quality, care and customer service. For all the sophisticated mechanisms used to conduct the range of service applications for fulfilling demanding specifications unique to the demands from a global composite of clients, President Jim Spalding says the company adheres to a “keep-it-simple†kind of philosophy. Simplicity would seem elusive given Spalding’s affirmation of an operational mandate for “perfect service and perfect quality.â€Â He says all of Stahl’s staff strives to have what is recognized as the “perfect†day. As Spalding explains, “That means you show-up at work on time, you make a quality part, treat customers like their number one, make a positive contribution wherever you are, maintain a clean working space and maintain our safety standards. It means zero defects and one hundred percent on-time delivery – that’s a perfect day.â€
When asked whether it is possible for an operation of such dynamics to actually achieve such perfection, Spalding does not hesitate in saying, “Absolutely.â€
“We have a lot of perfect days, but it all starts with the expectation. We have high expectations, and believe as a business we have to be perfect, but that doesn’t only relate to the way we’re treating customers and the way employees do their job, it also means that as a company we have to fulfill the expectations of our workers. Our leadership also has to be perfect, which means making sure we’re providing benefits, paying people accurately and on time, providing a good facility with good equipment and opportunities for employees to advance. We’re constantly operating on standards that have to be accurate. When you know what those standards are, it is simple to run a business,†affirms Spalding.
As an ISO-14001/ISO-9002/TS-16949-certified company, Stahl has devised unique systems to complement their capability to efficiently deliver large, complex, quality machined castings; parts that range from .5 pounds to more than 280 pounds in volumes of several hundred to more than 400,000 annually. Its current position in industry and market penetration is a testament to the precision and service standards that have been honed over 70 years, but to put that in proper context requires examination of just how far the company has come since its inception.
Stahlwartly Steadfast
Glen Stahl established Stahl Specialty in 1946 when he began operating from a small, rented workshop in Kingsville, Missouri. He initially stayed busy by producing sanding drums and lathe faceplates, but his business was soon boosted when the owner of Goodall Manufacturing (a producer of lawnmowers) asked Stahl to cast a “G†insignia which could be applied to his line of lawnmowers. As this professional relationship grew, Goodall would later ask Stahl the feasibility of casting a lawn mower deck for a new type of rotary mower, but in this era, the general industry consensus was that these decks were too large for casting in a permanent mold. Stahl, however, went on to create the tooling and over the next few years, these casting would account for almost all of production by the foundry. By the 1960’s, Stahl had branched out into an extensive range of castings which included housing for gas grills, pans, truck parts, playground equipment and more. Stahl didn’t turn-away from challenges, or opportunities, for that matter. Seeing the potential in value-added services, his became one of the first aluminum foundries to include in-house heat treating, and by 1965, the enterprise had its own tool & die facility as well as another facility for steel fabrication and machining, making it one of the first one-source-of-solutions within the industry. Customers grew as did job orders necessitating the establishing of a second location in Warrensburg, Missouri by 1970, but with the increasing burdens on production, Stahl and his team ultimately realized that the traditional manufacturing methods could neither keep pace with demand or accommodate the diversity of products in degree sufficient to maintaining the quality mandated by the company as well as its clients.
In order to achieve the desired efficiency and quality, while reducing lead times and inventories, the company implemented a methodology which is described as cellular manufacturing. The process calls for a compartmentalizing of production machines and personnel which collectively share similarities in their operational processes. In this case, each casting cell is tasked with specific jobs. For example, one cell would be dedicated to producing an inboard V6 exhaust pipe for Mercury Marine while in another cell, the team is focused on producing the 40-pound brake housing required by John Deere Company. Workers are empowered to take ownership of their respective cell as well as the components they produce. Each cell has access to their own unique equipment resources, whether that calls for the furnaces, the tilt-pour casting machine, saws or buffers, etc. The system essentially allows for increased efficiency, performance measuring and quality monitoring. Stahl Specialty Co. was a pioneer in the adopting and advancing of these operational techniques which are recognized as best practices today.
Stahl died in 1996 and the family sold their holdings in 2000, a transition which saw acquisition from such forces as ThyssenKrupp until a private equity group sold the company to another industry dynamo in Ligon Industries. Ligon, based in Birmingham, Alabama, is recognized as North America’s largest independent manufacturers of hydraulic cylinders, as well as a leading supplier of high definition aluminum castings through its holdings in more than a dozen different companies – and Stahl Specialty Co is a special contributor to that distinction.
Stahl Specialty Company Sales Manager Tom Browning, a 15-year veteran of the company who also considers himself as an unofficial historian and “keeper of records,†says he has enjoyed reading historical accounts that Glen Stahl and his wife maintained from the start of the company. Browning says Stahl’s wife credits her husband for “inventing†the processes which ultimately contributed to its corporate position today. However, Browning says, Glen Stahl was more modest, only claiming to “developing the processes.†In any case, as Browning says, “He helped make the company what it is today and he taught virtually everyone else in the world how to effectively produce aluminum castings. Our experience in doing this for so long has helped us maintain distinction as ‘the experts’ in this industry.â€
A Marvel in Motion
Given the range of components Stahl Specialty provides for automotive, heavy-duty diesel engines, marine, power generation and construction purposes, there is validation to President Spalding’s simple explanation that the company produces “products that move the world.† He says the company takes not only great pride, but also great responsibility in their role of supporting customers respective aims to drive forward, and those motions will prompt further advancements as well as opportunities for the company. Spalding says the migration to natural gas as a fuel in heavy-duty engines will enable Stahl Specialty to capitalize on systems in which their castings can be applied. He says their components will also increasingly become key contributors in the manufacturing of electric cars. Spalding adds that the industry emphasis on “green†technology will also lead to opportunities. As Spalding asserts, “Aluminum is green because it is completely recyclable… the products we make don’t end-up at the bottom of a lake, they can be used over and over again.â€
Spalding says Stahl will continue to focus on serving it North American market segment, even while it is shipping parts throughout the world. Stahl Specialty serves some of the biggest brand names, but it also partners with other great innovators of enterprise, including PreciseCast, a Colorado-based firm specializing in prototyping and engineering services who has recently earned distinction as “One to Watch†in industry.
Spalding says he is also especially encouraged to see significant business actually returning to the United States. With labor and transportation costs increasing overseas, as quality standards become increasingly suspect, many firms have discovered that the savings they initially perceived are simply not there. As these enterprises resource materials from manufacturers in America, rest assured this team in Missouri is prepared to deliver the goods.
By maintaining its mandate for perfect quality and perfect service, all while advancing the processes that result in increased efficiency, cost saving and value-added services, Stahl will not stall in its drive to keep America moving.
For more information, please visit their website at: Â Stahl Specialty Co.