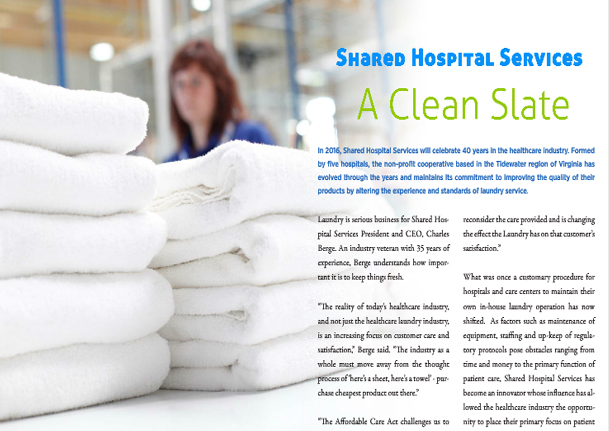
A Clean Slate
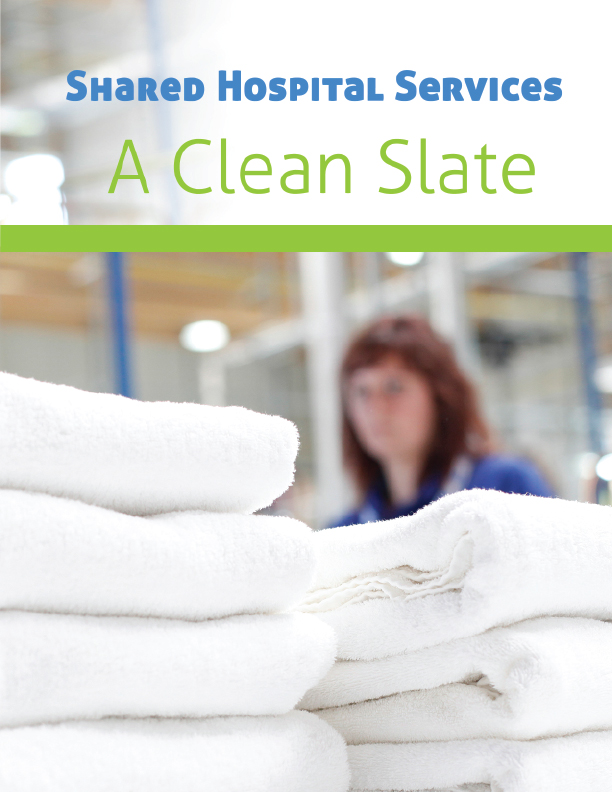
In 2016, Shared Hospital Services will celebrate 40 years in the healthcare industry. Formed by five hospitals, the non-profit cooperative based in the Tidewater region of Virginia has evolved through the years and maintains its commitment to improving the quality of their products by altering the experience and standards of laundry service.
________________________________________
Laundry is serious business for Shared Hospital Services President and CEO, Charles Berge. An industry veteran with 35 years of experience, Berge understands how important it is to keep things fresh.
“The reality of today’s healthcare industry, and not just the healthcare laundry industry, is an increasing focus on customer care and satisfaction,†Berge said. “The industry as a whole must move away from the thought process of ‘here’s a sheet, here’s a towel’ – purchase cheapest product out there.â€
“The Affordable Care Act challenges us to reconsider the care provided and is changing the effect the Laundry has on that customer’s satisfaction.â€
What was once a customary procedure for hospitals and care centers to maintain their own in-house laundry operation has now shifted. As factors such as maintenance of equipment, staffing and up-keep of regulatory protocols pose obstacles ranging from time and money to the primary function of patient care, Shared Hospital Services has become an innovator whose influence has allowed the healthcare industry the opportunity to place their primary focus on patient care and wellbeing.
“Healthcare is changing and becoming more outpatient care and there are more surgery centers. Therefore a cooperative laundry or a healthcare laundry in today’s industry will not survive, sole processing hospital laundry,†Berge said.
Guided by a Board of Directors representing various healthcare organizations in the region, Shared Hospital Services provides economies of scale that help their long-standing partners secure services, savings, efficiencies and enhanced safety measures through automation and mechanical technology implementation.
New to the position, Berge has begun to instill his philosophy within the organization.
“We’ve been going through a maintenance push for the last eight months. This has entailed getting the equipment back up to where it needs to be,†he said. “We have the automation and have added individual pieces to help us become more productive. Although old technology but new to us – the RFID chipping of specialty garments and specialty products ensures we can better serve our customers with accountability of product.“
“We want to protect ourselves, also,†Berge continued. “If the customer has something that they’re purchasing and they want us to wash as a specialty good, we can track it and know that it arrived at the laundry and we delivered it back. We are looking at that kind of technology.â€
HEALTHCARE LAUNDRY ACCREDITATION COUNCIL (HLAC)
Handling and processing more than 15 million pounds of laundry a year, Shared Hospital Services relies heavily on its 100 employees ranging from the laundry and production facility to the plant and delivery team. With no plans to expand from outside of their current 50-75 mile radius in Portsmouth, Virginia, the organization has the ability to take on additional poundage, but will choose a calculated, customer and people centric approach to growth.
“When a patient comes to the hospital they’re ill, – that is the reason they’re there,†Berge said. â€How do I affect their overall experience? They’re lying on my sheet, their head is on my pillow case, my blanket covers them, so it is important these products delivered to them are processed properly, meet all of the HLAC requirements but also be a quality product that the patient will feel comfortable with.â€
Centrally located within the market they serve, Shared Hospital Services works closely with the Healthcare Laundry Accreditation Council (HLAC) to ensure that workers are adhering to safety standards and that the laundry is producing clean linens. A voluntary venture, the accreditation provides a comprehensive audit of operational processes, equipment and employee practices. Following these guidelines prompts the organization to do more.
“Shared Hospital Services is striving to improve the quality of our products. Since I have been here we’ve done a big influx of new pillow cases and sheets and am looking at alternative products that we haven’t used before to help give the patient a better experience,†Berge said.
NEW CULTURE OF CLEAN
Leading an organization with a pedigree and history of success like Shared Hospital Services has urged Berge to establish a new culture within the laundry industry. By creating an atmosphere where employees respect one another and work together to achieve common goals on a daily basis, it creates a rewarding culture where individuals are respected and revered for their efforts.
“At the beginning of the day, the biggest asset I have isn’t the linens or the equipment, it’s the employees,†Berge said.
“I want to create opportunities for our employees to advance. For them to understand ‘if I work hard, there’s something else for me to do’. The more responsibility, my feeling is, the more fiscal reward there should be for that position as well. It creates a better atmosphere in your operation.â€
Instigating a number of employee-based committees – from safety to wellness, Shared Hospital Services dynamic outlook for its organization does not solely rely on fiscal rewards to applaud and appreciate its core group. By pushing for more employee involvement in the decision making processes, Berge hopes to bring health to the forefront.
“One issue we all face is health care and health care insurance costs. We’re no different than anybody else. Our desire is to provide all employees with a better understanding of their health benefits and how to better use benefits offered to produce a healthier work force,†he said.
“At the end of the day people have to buy into wellness,†he continued. “It isn’t something you can make people do; you can’t be better unless you know what the problems are. We encourage all employees to take advantage of their free annual check-ups and assist them where and whenever needed.
By affording employees the opportunity to receive proper treatment, Berge and Shared Hospital Services are dedicating themselves to the wise words of Mahatma Ghandi, who said: “it is health that is real wealth and not pieces of gold and silverâ€. But as the CEO, Berge acknowledges that small steps equate to small victories.
“We desire a healthy workforce. However you can’t manage what you don’t know,†Berge said. “My first goal is to see if I can encourage my employees go to the doctor. We will make it available to them.â€
“I want to eliminate all the excuses. I don’t want to hear ‘I can’t take time off or I don’t have transportation’. We will give you the time off; I will pay you to go see the doctor. We will do it during your work day because you’re valuable to me.â€
A FRESH FUTURE
As General Manager and President at Shared Hospital Services, Berge’s responsibilities and goals are far-reaching and over-arching. On the operations side, Berge hopes to increase efficiency, but it is his selfless approach to running an organization that shines brightest moving forward.
“Most importantly I want to instill an atmosphere in the laundry of advancement and potential to move forward. This should be a place where people want to come to work,†he said. “We have to educate our employees and promote from within. The biggest success I can have is an employee that is ready to advance, and encourage them to go after that position.â€
“The laundry industry needs youth brought into it. I feel one of my responsibilities is to bring the next generation into laundry and train them,†he continued. “The laundry industry is a great industry. I’ve been in it for 35 years, and it’s treated me well. My goal is to instill an education and training facility. We want to have growth, be efficient and I would love this organization to be double the size in 10 years.â€