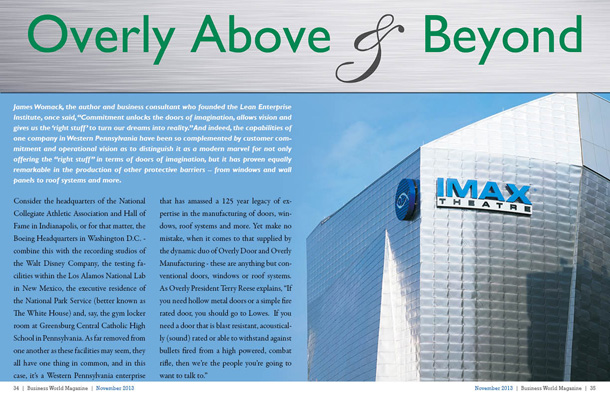
Overly Above and Beyond
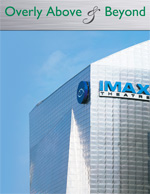
James Womack, the author and business consultant who founded the Lean Enterprise Institute, once said, “Commitment unlocks the doors of imagination, allows vision and gives us the ‘right stuff’ to turn our dreams into reality.†And indeed, the capabilities of one company in Western Pennsylvania have been so complemented by customer commitment and operational vision as to distinguish it as a modern marvel for not only offering the “right stuff†in terms of doors of imagination, but it has proven equally remarkable in the production of other protective barriers – from windows and wall panels to roof systems and more.
Consider the headquarters of the National Collegiate Athletic Association and Hall of Fame in Indianapolis, or for that matter, the Boeing Headquarters in Washington D.C. – combine this with the recording studios of the Walt Disney Company, the testing facilities within the Los Alamos National Lab in New Mexico, the executive residence of the National Park Service (better known as The White House) and, say, the gym locker room at Greensburg Central Catholic High School in Pennsylvania. As far removed from one another as these facilities may seem, they all have one thing in common, and in this case, it’s a Western Pennsylvania enterprise that has amassed a 125 year legacy of expertise in the manufacturing of doors, windows, roof systems and more. Yet make no mistake, when it comes to that supplied by the dynamic duo of Overly Door and Overly Manufacturing – these are anything but conventional doors, windows or roof systems. As Overly President Terry Reese explains, “If you need hollow metal doors or a simple fire rated door, you should go to Lowes. If you need a door that is blast resistant, acoustically (sound) rated or able to withstand against bullets fired from a high powered, combat rifle, then we’re the people you’re going to want to talk to.â€
Overly specializes in the manufacturing of protective barriers. From acoustic doors and windows that help block out sound used by major recording studios and doors that can withstand extremes in pressure or thermal fluctuations used by nuclear plants, research centers and industrial facilities throughout America, to the metal roofing systems that not only grace the White House, but that which enhances the architectural integrity and aesthetic allure of institutions such as the Milwaukee Art Museum, the Texas State History Museum, the Ronald Reagan National Airport, the Houston Astrodome, Boston’s IMAX Theatre, Old Main at Wayne State University and the Knowledge Center at the University of Nevada – these represent just a fraction of the infrastructure to which Overly has contributed in its service to convention centers, museums, universities, industrial sites, municipal buildings, transportation hubs, and so much more. Yet in so doing, Overly imparts the same attention to detail in exacting its delivery of the same degrees of quality whether that work involves a large project or a small project. As Reese affirms, “The doors we put in the locker room at Greensburg Central Catholic High School are just as important as the doors that we create for the Lawrence Livermore National Laboratory.â€
Of course, creating the doors that prevent sounds of a school gym from penetrating the confines of a locker room may seem far less critical than, say, the work Overly performed for Los Alamos (a project that involved creating a thermal barrier involving a 4-foot thick door and frame that weighed more than 16,000 pounds), but to Reese’s point, the company takes great pride in its work, customer interactions and ability to overcome engineering challenges large and small. And to be sure, in many cases, Overly’s products are engineered to specifications essential for fulfilling critical functions, and whether that’s a bullet proof window, fire door or some other kind of thermal and pressure resistant barrier, employees of Overly exercise remarkable attention to quality and performance standards because, as Reese says, “If our barrier doesn’t work, someone might actually be killed.†This very fact was communicated during an episode of the History Channel’s Modern Marvels program, a broadcast that demonstrated Overly’s precision in developing products that can withstand against heat, pressure and impact from bullets. In one demonstration, Overly’s lowest rated door withstood blast from a 235 mph gust of wind, velocity that is significantly greater than the highest surface wind-speed ever recorded. While Reese fully understands how these kind of protective barriers serve in coastal communities that encounter hurricanes, he acknowledges that in some cases, he isn’t so gifted with awareness as to how his company’s products are serving in terms of other applications. For instance, in creating massively thick doors and assemblies for institutions like Lawrence Livermore and Oak Ridge National Laboratories, he once occasioned to ask an engineer what exactly was going on behind the doors to necessitate the use of so much steel. “The engineer told me I would sleep a lot better at night if I didn’t know,†says Reese.
A Legacy of Innovation
Overly origins date back to 1888, when a metal smith known as Overly opened a small firm in Greensburg, Pennsylvania. As a sheet metal worker (or tin-knocker as they were known) his company garnered a reputation for producing marquis or spires for area churches, and continued in that capacity for several decades until the advent of fire doors. The early varieties of fire doors were tin-clad (wooden doors complemented with a metal veneer) and Overly was among the very first in the industry to achieve UL approved fire rating. The company soon became a leading manufacturer of fire doors, but continued to take on other sheet metal projects. Then in the 1930s, in that era of The Great Depression, the Overly Family came upon hard-times like so many others which ultimately resulted in selling the company to the Wehe Family who was also from Greensburg. CEO Homer Wehe guided Overly Manufacturing for more than 40 years, advancing beyond the fire door and spire production to establishe a new proprietary metal batten roof system. The company would go on to service an impressive client and project list which includes the Heinz Chapel at University of Pittsburgh, the re-roofing of the Houston Astrodome, and the roofing of the Pentagon, to name just a few projects.
Over the last 25 years, there can be no overstating of Reese’s impact in leading the company through a remarkable evolution in terms of engineering expertise, operational prowess, production efficiency and market presence. Much has changed since Terry Reese and his Brother David purchased the company from the Wehe Family. To put that in proper perspective, it is important to know that there was nothing in the way of steel fabrication or engineering that figures in Reese’ professional background. Ironically, so much of what Reese has imparted in advancing Overly’s manufacturing processes and market penetration came from his experience in another line of work which seems worlds apart from his current endeavors. Ironically, Reese is a former owner of a Pepsi Franchise. As far as comparisons go, there is little similarity between his role with Pepsi and that of Overly with the exception of the fact that just as Pepsi is sold to retail businesses who supply the product to end consumers, the products manufactured by Overly are likewise sold to businesses in the form of door and hardware distributors, contractors, architects and engineering design firms. And while Pepsi may be the taste of a new generation, Reese’s professional acumen certainly flavored the formula for a new era of engineering at Overly. That all began when Reese and his brother sold their franchise and began looking to acquire a new business, a two year process that had them conferring with various investment firms and business brokers, but failing to find the right fit. “We were looking for a company where we felt we could add value … we wanted it to be a company that produced a tangible product, not something in the service industry, but a company that made something, that was a number one or strong number two in its business segment… something in an industry where there was some barrier to entry because it required specialty knowledge or testing, something not anybody could just go and do,†explains Reese. One morning, a next door neighbor happened to mention that Overly was about to be sold by the Wehe family and Reese ultimately went on to purchase the company, liking all he saw in its history, product offerings as well as the work ethic and craftsmanship of the company’s workforce, and what was more, the company was located right there in his hometown of Greensburg.
At this time, the company still functioned as something of a job shop which was difficult to reconcile for someone coming from a production stream rich and marketing rich environment like Pepsi. Reese and his brother implemented a new national sales strategy where none existed, restructured plant operations as well as the company to create a new production system as well as separate divisions, with one that solely focused on doors and assemblies (Overly Door) and another division that could grow by reinvigorating the work involving roof systems and other products (Overly Manufacturing). As Reese explains, he and his brother also met with engineers to determine if products could be redesigned to improve their function. As can be imagined, it prompted some measure of angst with engineers when he asked, “Can we do it better?†Reese, who has no qualms admitting that he doesn’t ascribe to conventional wisdom, says sometimes companies get steeped in a mindset that compels a belief that things can only be done a certain way. In this case, engineers explained that they deal with metal and therefore, must weld. Reese considered how glue was being used to hold airplane wings together and how industrial tape was used to keep UPS trucks together. “We understood liquids, not solids … so when they said, ‘We weld’ we said, ‘Why?’ … There are other ways to create a bond. Why can’t we look into those methods?â€
From that simple inquiry a lot of complicated science followed which culminated with the company patenting an entirely new type of manufacturing process essential to creation of acoustic doors and blast resistant doors and both incorporate adhesives as opposed to welding. These innovations not only reduced finishing time and operating costs but resulted in products that were stronger, more durable and better performing.
Other efficiencies would be realized through the incorporation of digital design solutions. Though it may be difficult to imagine, there was a time the company only used AutoCAD for marketing purposes. When Reese arrived, engineers were still using paper and a pencil to design every project from scratch, in fact, some balked at the design technology insisting they could work faster by using a pencil. “If I told them to go back to pencil drawing today they might shoot me,†laughs Reese.
As for other changes, these involved expanding training across product platforms and the fostering of greater collaboration and communication between varying work teams. “We had to develop our people, train them, and we had to trust them. That was another difference we brought,†says Reese. “The old owners of Overly were very top down and directed everything. The owner told us, ‘When I leave, you’re going to have to get four guys to replace me.’ Our philosophy was there were people who’ve been here 25 years and they may have ideas on how to do things better… we created work groups where we discussed projects and designs, and as we gradually moved away from the formal, communications began to flow and engineers were able to service their thoughts … there’s been a real change in having a management team consisting of senior employees who don’t just take direction and execute, but are empowered to anticipate, to be part of the creative process… it results in a different level of engagement.â€
Overly has grown by acquiring a company known as Tiger Door, and today it has a production plant in Mexico as well as an expanded facility in Greensburg. The company’s reputation for high performing, engineered innovations, as well as professional integrity and ISO-certified quality has also grown internationally. In addition to serving an impressive list of clients, the company is aligned with an equally impressive list of suppliers, which includes industry dynamos such as Contrarian Metal Resources and Spectrum Metal Finishing. In sourcing suppliers, Reese says the company has never focused on finding the cheapest prices, but rather connecting with those whose quality standards are as consistent as those compelling operations at Overly. That quality is reflected in infrastructure throughout the world and whether it is a roof made from stainless steel, copper, titanium or some other metallic marvel, Overly stands by its manufacturing offering a guarantee of 30 years. As Reese says, “If you’re not going to hold the building for at least fifty years, you don’t want an Overly roof.â€
Door to the Future
As for the future, Reese says the company has recently been recertified to supply products to the nuclear industry, and he anticipates Overly will continue servicing in this industry sector as a new generation of nuclear plants grow throughout the world. On the roofing side of the business, Overly has started a new venture in the developing of wall panels which Reese believes will elicit further success. The company continues to maintain a strong market presence in the supply of acoustic doors and blast resistant doors which has represented the fastest growing segment of the business. Yet for all of the Overly companies’ success and potential for the future, family is also at the forefront of Reese’s considerations. Reese is also the first to admit that family is one of the things that excites him about the future.
As a father of three children who pursued their own respective career paths, Reese expresses noticeable pride when explaining that each ultimately resolved to return to Greensburg and are fulfilling important roles within the company. His Daughter Heather is Vice President of Operations for Overly Manufacturing, Son Tyler is Vice President of Operations for Overly Door and Son Jonathan is Vice President of Sales for both companies.
“What excites me is to see how much better they are than I was when it comes to day to day operations … they really understand what they’re doing and over the last few years, though we’ve always been a high quality manufacturer, I’ve seen us become more rejuvenated,†says Reese. He adds that the next generation of workers can also be found operating within the plant. “We have the next generation of people at all levels … a critical mass for the next 15 to 20 years. We’ve got all the pieces in place and the only thing that held us back for a time was the national economy, but it forced us to become leaner, more efficient and more flexible. Today, we’re leaner and better than ever.â€
Another contributing factor working for the benefit of Overly is the simple fact that their work is so specialized. Whether it’s a radiation shield for a nuclear plant, a bullet proof door or window, or metal roof capable of withstanding hurricane winds, these are products which undergo rigorous testing and must comply with exacting standards of certification before ever entering the market. As Reese says, “We have very highly specialized people who produce highly specialized products … it’s not like anyone can just open a new business and do what we do.â€
For more information, please visit their website at   Overly Door Company
Preferred Vendors of Choice: